O que a empresa realmente precisa fazer para garantir o desempenho do campo fabril, aumentar a produção, otimizar os reparos, reduzir custos e evitar desperdícios? A pergunta até pode parecer complicada, mas a resposta é simples: Planejamento e Controle de Manutenção, o famoso PCM!
O PCM, como também é conhecido, é a prática responsável por alinhar todo o processo de manutenção. E serve para garantir a usabilidade e confiabilidade dos ativos, reduzir desperdícios e tornar a produção mais lucrativa.
Máquinas e equipamentos defeituosos tendem a gerar custos e exigem muito tempo de serviço. Então, se a empresa não possui um Planejamento e Controle de Manutenção para gerenciar tudo do setor, pode ser que ela sofra com gastos elevados e desnecessários.
Que controlador de manutenção quer correr esse risco? Nenhum!
Como o PCM é um dos temas mais importantes dentro do universo da gestão da manutenção, explicar toda a sua complexidade em apenas dois ou três parágrafos é impossível. Assim, resolvemos escrever esse post para abordar tudo que é preciso saber sobre o tema.
Preparado para esclarecer todas as dúvidas relacionadas ao Planejamento e Controle de Manutenção?
O que é PCM e por que ele é importante?
O PCM é um conjunto de tarefas que visa garantir a disponibilidade e confiabilidade dos ativos e reduzir os custos de manutenção.
Independentemente do segmento da empresa, seja construção civil, logística, manufatura ou agronegócio, todo mundo sabe que o mercado esta mais competitivo. E que assegurar uma produção livre de erros pode ser determinante para entregar um diferencial e sobressair.
Ou seja, o Planejamento e Controle de Manutenção é importante para a empresa garantir a usabilidade, segurança e confiabilidade dos seus ativos. E, com isso, preparar o chão de fábrica para atender a demanda com excelência e agilidade.
Estrutura do planejamento e controle de manutenção
Como o PCM envolve muitas atividades, sua estrutura é dividida basicamente em três etapas: planejamento, programação e controle da manutenção. Abaixo explicamos melhor cada um deles:
Planejamento da manutenção
O planejamento consiste em documentar todos os serviços, recursos, processos e materiais necessários para realizar a manutenção. O objetivo dessa etapa é criar e gerenciar planos específicos para cada tipo de ativo, a fim de garantir sua disponibilidade.
Existem seis tipos de planos no planejamento:
1. Plano de Manutenção Preventiva
O plano de manutenção preventiva visa impedir falhas que podem levar um determinado ativo a parar e interromper a produção. O documento deve conter os seguintes dados:
- Checklist da manutenção: todos os procedimentos já realizados em cada equipamento;
- Custos: gastos com materiais, peças, contratação de profissionais, inclusive sistemas de gestão;
- Cronograma: a frequência e periodicidade para realização de revisões, consertos e reparos;
- Equipe: quantidade de profissionais responsáveis pela manutenção, bem como as qualificações necessárias;
- Atividades: definir as funções de cada profissional com base nas suas qualificações.
Depois que o documento estiver estruturado e a equipe for direcionada, o controlador deve acompanhar o progresso da manutenção preventiva e os indicadores-chave de desempenho para assegurar a qualidade e eficiência dos serviços.
2. Plano de Manutenção Preditiva
A manutenção preditiva tem como objetivo prever falhas e impedir a deterioração de um equipamento. Para estruturar esse plano será necessário:
- Identificar os ativos críticos: definir quais máquinas e equipamentos serão incluídos no programa de manutenção. Nesse caso, os melhores candidatos costumam ser os ativos de criticidade alta. Ou seja, essenciais para a produção.
- Informações sobre a máquina: dados relevantes que oferecem insights sobre o comportamento de cada ativo crítico;
- Análise dos ativos: verificar o desempenho dos ativos e determinar seus modos de falhas.
- Previsões: entender e prever as falhas com base nos dados coletados para a análise.
Depois de estruturar o documento, a empresa deverá executar o plano e monitorar a manutenção para certificar melhorias significativas nas operações.
3. Plano de Inspeção Sensitiva
O plano de inspeção sensitiva identifica possíveis indícios de falha por meio de análise instrumental. O documento deve conter informações detalhadas para a execução da manutenção e estabelecer uma previsão dos riscos de falhas.
Para esse plano é necessário:
- Definir a atividade: que manutenção será realizada no ativo, se preventiva, sistemática, preditiva ou prescritiva.
- Periodicidade: períodos em que deverá ser realizada a manutenção, considerando a frequência de uso do ativo.
- Mão de Obra: avaliar a tarefa a ser realizada e qual o profissional mais bem preparado para concluir a manutenção.
- Pontos de Inspeção: definir o equipamento que será inspecionado e quais pontos.
4. Plano de Lubrificação
Esse plano objetiva manter a saúde dos ativos em dia com relação à lubrificação. É crucial para evitar o desgaste prematuro de peças, bem como outros componentes. Elaborar esse documento não é difícil, porém é preciso seguir os seguintes passos:
- Mapear as máquinas e equipamentos: definir os ativos que devem fazer parte do plano de lubrificação;
- Identificar os pontos a serem lubrificados: esclarecer quais partes do ativo vão receber lubrificação;
- Definir o tipo de lubrificante: estabelecer o produto que será utilizado, bem como a quantidade necessária.
- Verificar aplicação e tempo de lubrificação: definir quais profissionais serão responsáveis pelo serviço e qual é o período de duração para lubrificar o ativo;
- Ter controle de estoque: para que a lubrificação ocorra conforme o planejado, a empresa precisa se certificar de que o estoque de produtos está em dia e dentro do prazo de validade;
- Identificar falhas: apontar as falhas que estão ocorrendo por falta de lubrificação e programar ações para corrigi-las.
5. Plano de Calibração
Nesse plano são definidas as atividades a serem executadas no momento da calibração. O documento deve mostrar informações sobre o serviço, bem como os ativos calibrados.
Abaixo, veja as informações que devem constar no documento:
- Data de calibração;
- Data planejada;
- Código do equipamento;
- Laudo inicial e final;
- Função.
6. Plano de Melhorias
O plano de melhorias tem como proposta melhorar o desempenho do parque fabril. Envolve estabelecer metas e ações a serem realizadas, bem como o período limite para atingimento dos objetivos.
Para elaborar esse plano será preciso:
- Entender o problema: colocar no papel todos os problemas que estão prejudicando o desempenho das máquinas e equipamentos;
- Analisar o comportamento atual da empresa: verificar como a empresa está se comportando para solucionar os problemas.
- Mobilizar a equipe: conversar com os operadores e demais profissionais da manutenção para levantar ideias e sugestões de melhorias;
- Definir metas: estabelecer os objetivos que devem ser alcançados e o que será necessário para o alcance das metas
Programação da manutenção
Se o planejamento consiste em documentar os serviços, recursos, processos e materiais necessários para a manutenção, a programação envolve tirar todas as ideias do papel e colocá-las em prática. Assim sendo, implica em agendar e definir um cronograma para executar os serviços.
Se o objetivo é fazer uma programação correta, o controlador precisa prestar atenção aos seguintes pontos:
1- Produtividade da mão de obra
Não adianta programar a manutenção, se o chão de fábrica não possui profissionais suficientes para realizar as tarefas. O ideal é que, antes de elaborar o cronograma, o responsável meça a produtividade da equipe e veja quando haverá disponibilidade.
2- Atividades pendentes
Quais atividades já foram programadas e qual o seu nível de urgência? Se não quer que outras tarefas sejam atrasadas, certifique-se de que a nova programação não vai interferir nos serviços já agendados.
3- Definir prioridades
É possível garantir uma produção livre de pausas se o controlador programar a manutenção de forma estratégica. Na fábrica existem equipamentos mais e menos críticos, então definir as prioridades com base no grau de criticidade de cada ativo é importante para garantir a continuidade da produção e impedir paradas não programadas.
Controle da Manutenção
O controle consiste em medir tudo o que foi feito nas etapas de planejamento e programação. Para conseguir mensurar os resultados, será preciso recorrer a métricas e indicadores-chave de desempenho (KPI). Os números vão ajudá-lo a compreender o que pode ser melhorado, inclusive como a manutenção tem beneficiado o parque fabril.
Existe uma série de indicadores que podem ser utilizados para o controle da manutenção. Mas, aqui, citaremos apenas os principais:
Availability (A)
Availability, também conhecido como disponibilidade de ativos, é um indicador que mostra o tempo que uma máquina ou equipamento está pronto para realizar suas operações. O resultado é dado em percentual, por isso quanto maior o valor, melhor.
Abaixo, veja a fórmula:
O MTBF e o MTTR são indicadores importantes para medir o período entre as falhas e o tempo necessário para corrigir um problema. A seguir, explicamos melhor cada um deles.
MTBF
MTBF é um indicador que mostra o tempo médio entre duas falhas de um ativo. Essa KPI também é importante para o controle da manutenção, pois ajuda o operador a medir a confiabilidade de uma máquina.
Para achar a MTBF, usamos a seguinte fórmula:
“TD” seria o tempo total de disponibilidade de um ativo, enquanto que “TM” o tempo total da manutenção. Já o “P” representa o número de paradas.
MTTR
MTRR é um indicador que mostra o tempo médio que a equipe de manutenção leva para colocar o ativo em funcionamento. Ou seja, mede a habilidade e desempenho dos trabalhadores.
Para realizar o cálculo, usamos a equação:
Backlog
Backlog, que em português significa “acúmulo”, é um indicador que mede o tempo de execução da manutenção com a mão de obra disponível. Como novas demandas surgem a todo momento, seu resultado pode variar no decorrer do dia.
Para descobrir esse indicador, usamos a seguinte equação:
Na primeira parte da fórmula, o controlador deve somar todas as ordens de serviços (planejadas, pendentes, programadas e executadas). Depois, dividir esse valor pelo homem-hora. Para descobrir o HH disponível, deve-se multiplicar o número de pessoas atribuídas a uma tarefa pelo seu tempo de duração.
Benefícios do Planejamento e Controle de Manutenção (PCM)
O grande diferencial do Planejamento e Controle de Manutenção é que ele ajuda (e muito) na redução dos desperdícios. Mas isso está longe de ser a única vantagem. Ao aplicar o PCM no setor, a empresa é capaz de garantir outros benefícios incríveis como:
- Otimização de recursos: com todas as informações coletadas é possível evitar o consumo excessivo de materiais, bem como destinar melhor os recursos para manutenção.
- Redução das paradas: o planejamento, programação e controle ajudam na redução de falhas e paradas não programadas;
- Mais qualidade: com os ativos funcionando corretamente, a todo vapor, a empresa consegue garantir mais qualidade nos processos, produtos e serviços.
- Maior segurança no campo fabril: o planejamento e a programação ajudam a instruir e direcionar melhor as equipes da manutenção, reduzindo riscos de acidentes.
Dicas práticas para implementar o PCM no setor
Certamente, aplicar o PCM pode ser desafiador por conta da complexidade das etapas, processos e pessoal envolvido. No entanto, não se apavore! Abaixo separamos algumas dicas que podem ajudá-lo a implementar o Planejamento e Controle de Manutenção dentro do seu setor. Confira!
1- Entenda os diferentes tipos de manutenção
Cada manutenção possui um objetivo diferente. A manutenção preventiva busca prevenir falhas nos equipamentos, enquanto a manutenção preditiva determina antecipadamente a necessidade de consertos e reparos. Já a manutenção corretiva serve para restaurar o ativo.
Entender os diferentes tipos de manutenção ajuda na elaboração do planejamento e cronograma, também no direcionamento das tarefas.
2- Treine a sua equipe
Os colaboradores serão responsáveis por realizar as tarefas de manutenção. Logo, deve-se investir na qualificação desses profissionais para assegurar que todos os serviços sejam realizados com excelência.
3- Invista em tecnologia
Fazer todo planejamento e controle na ponta do lápis não parece uma ideia interessante. Hoje é preciso tomar decisões e concluir as tarefas com o máximo de agilidade, caso queira sobressair. Então o ideal é que a empresa invista em tecnologia para acelerar todos os processos de manutenção.
Se você ainda não conhece uma ferramenta capaz de fazer isso, convidamos você para testar o Keepfy gratuitamente por 7 dias. Nesse período de teste você poderá acessar funcionalidades inovadoras que simplificam o Planejamento e Controle de Manutenção, e que contribuem para a tomada de decisão estratégica.
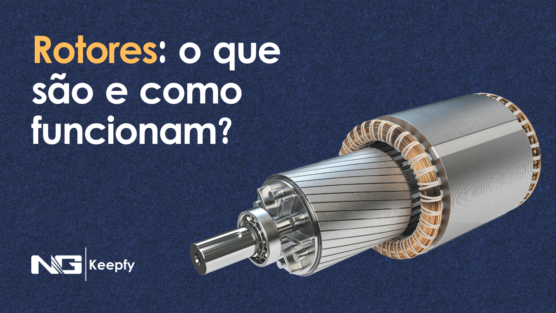
Rotores: o que são e como funcionam?
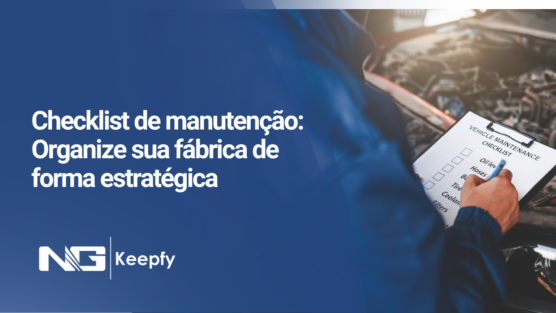
Checklist de manutenção: Organize sua fábrica de forma estratégica
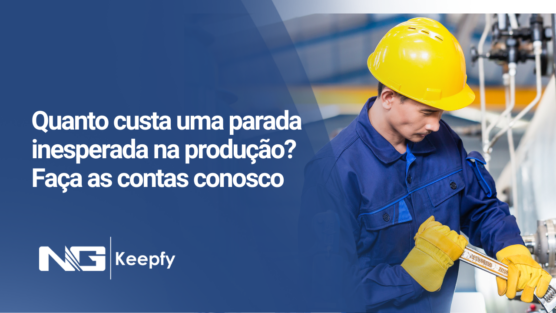
Quanto custa uma parada inesperada na produção? Faça as contas conosco
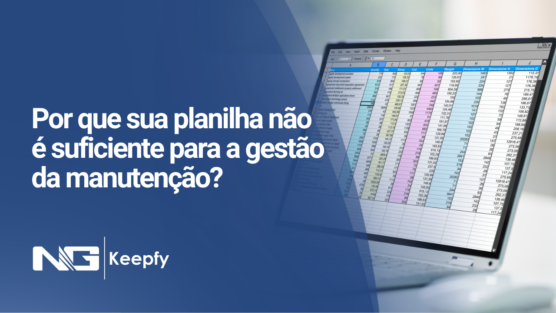
Por Que Sua Planilha Não É Suficiente para a Gestão da Manutenção?
Conta pra gente!
o que você achou deste conteúdo? Escreva nos comentários.
Boa tarde ,fico feliz pelo rico conteúdo apresentado Keepfy, ,solicito por gentileza informações se este aprendizado vocês fornecem certificado de conclusão do curso,