Quando falamos sobre manutenção industrial, uma das principais dificuldades encontradas pelos gestores é conseguir aumentar a qualidade e confiabilidade dos ativos. Para resolver essa questão, a metodologia 8D pode ajudar!
O método foi criado justamente para solucionar a causa raiz dos problemas. Evitando, assim, falhas e erros recorrentes.
Quer entender melhor sobre como funciona essa ferramenta? Então continue a leitura e veja tudo o que você precisa saber sobre o assunto!
O que é a metodologia 8D?
A metodologia 8D foi criada ainda no século passado, pela Ford Motor Company, e desde essa época vem sendo aplicada por diferentes tipos de empresas. Existem, inclusive, estudos acadêmicos sobre o tema.
De acordo com um artigo publicado pela Revista S&G, da Universidade Federal Fluminense, o 8D é excelente para alcançar a melhoria de processos e produtos.
Basicamente, a ferramenta traz oito passos, também chamados de disciplinas, que devem ser seguidos para impedir que um problema continue acontecendo. Assim, o objetivo é identificar o que está causando aquele problema. Ou seja, a sua causa raiz.
Uma vez identificada a causa, é possível planejar ações imediatas para resolver o problema. O foco é garantir que o mesmo erro não se repita futuramente, o que pode ser muito útil para o sucesso do parque fabril.
Na década de 90, foi incluído mais um passo, o D0, que viria antes de todos os outros. Entretanto, o nome não foi alterado e mesmo com as nove etapas continua sendo chamada de metodologia 8D.
As 8 disciplinas do 8D
Abaixo, iremos detalhar cada uma das 9 disciplinas da metodologia 8D. Vamos lá?
D0 – Criação de um plano para resolver o problema
Em primeiro lugar, é de extrema importância que seja criado um planejamento das atividades para definir o que é necessário para alcançar o objetivo. Aqui é interessante fazer uma estimativa de quanto tempo será gasto e quais os custos envolvidos.
Também é indicado registrar todas as informações básicas, pois isso vai agilizar o trabalho.
D1 – Composição de uma equipe
A formação do time que vai atuar na aplicação da metodologia é um ponto-chave para que tudo ocorra como o planejado. Todos devem ter o mesmo interesse em alcançar a meta, mas também é interessante que as pessoas envolvidas tenham perfis diferentes para que possam contribuir com visões e ideias novas.
D2 – Descrição do problema
Aqui, a equipe vai reunir todas as informações disponíveis acerca do problema, procurando descrever o erro com o máximo de detalhes possível. O foco é entender com clareza qual a raiz da falha.
Uma ferramenta que pode ser usada nessa etapa é o 5W2H, que ajuda a compreender melhor a situação e a criar um plano de ação. O gestor deve responder o que será feito, porquê, onde, quando, por quem, como e quanto vai custar.
D3 – Elaboração de um plano rápido para a contenção do problema
Na disciplina três, a empresa ainda não tem definida uma solução permanente, mas pode elaborar um plano provisório. Ou seja, uma ação rápida que pode ser feita para conter o problema.
Ao priorizar essa ação, a empresa consegue mitigar os danos e impedir que o problema continue acontecendo.
D4 – Identificação da causa raiz
Uma vez que consegue conter o problema, é hora da empresa analisar o erro com maior profundidade. Isso para identificar a causa raiz e o motivo que gerou a falha.
Para auxiliar nessa disciplina, o gestor pode aplicar a ferramenta dos cinco porquês, em que é questionada a razão do problema cinco vezes até identificar a causa. Ou o diagrama de Ishikawa, que é um gráfico usado para encontrar a causa do erro.
D5 – Seleção e verificação de uma solução
É na quinta disciplina que o profissional vai selecionar qual solução irá implementar para resolver o problema. Além disso, é aqui que a empresa deve iniciar a aplicação e avaliar se essa é a solução ideal.
Não importa se a equipe descobrir que outra solução seria mais eficiente, essa etapa serve justamente para ter certeza da escolha feita.
D6 – Implementação de uma solução que seja permanente
A sexta disciplina é constituída, basicamente, pela implementação de uma solução permanente para solucionar o problema enfrentado pela empresa. Após implementá-la, o gestor deve fazer um acompanhamento para ter certeza de que está funcionando.
D7 – Prevenção para impedir o reaparecimento do problema
Com o problema resolvido, é a hora de prevenir que o erro ou falha não aconteça futuramente. A equipe deve, portanto, propor formas de evitar que o mesmo problema venha a se repetir, desde mudanças estruturais a alterações menores.
D8 – Comemoração dos resultados
Por fim, é hora da empresa comemorar os resultados alcançados, reconhecendo a dedicação e esforço de todas as pessoas envolvidas.
Quando utilizar a metodologia 8D?
Para quem trabalha com manutenção de ativos, a metodologia 8D sempre deve ser utilizada para identificar a existência de um problema recorrente. Ou, até mesmo se um problema surgir pela primeira vez, mas o gestor acredita que pode se repetir.
Em geral, a ferramenta é utilizada sempre que é preciso solucionar um problema na empresa. Principalmente nos casos em que a não resolução pode trazer um impacto significativo nos resultados operacionais e financeiros.
Como aplicar a metodologia 8D na manutenção?
A aplicação da metodologia 8D é simples: basta colocar as disciplinas em prática. Existem alguns profissionais especialistas na metodologia que oferecem consultorias para ajudar, mas se a empresa seguir o passo a passo acima não existe essa necessidade.
Colocar a metodologia em prática pode ser um pouco trabalhoso, mas os resultados valem a pena e podem trazer benefícios que superam a continuidade de processos como, por exemplo, maior qualidade do produto, satisfação de clientes e aumento de competitividade.
Agora que você já aprendeu o que é a metodologia 8D e como aplicá-la na sua empresa, aproveite para conferir mais conteúdos sobre manutenção industrial no blog da Keepfy!
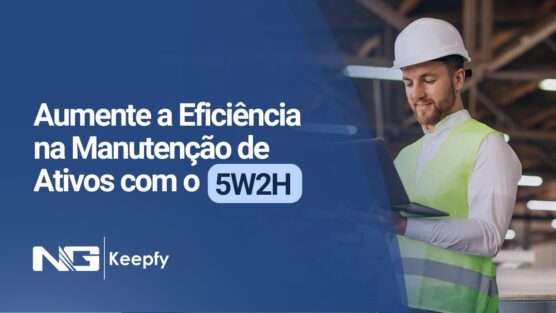
Aumente a Eficiência na Manutenção de Ativos com o 5W2H
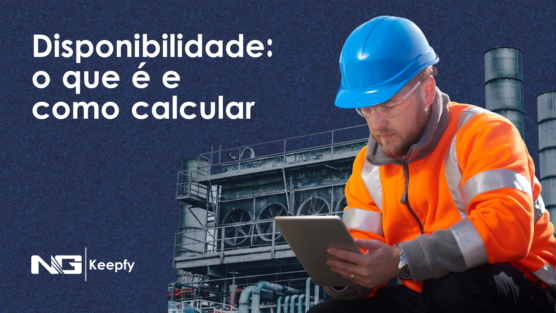
Disponibilidade: o que é e como calcular na manutenção
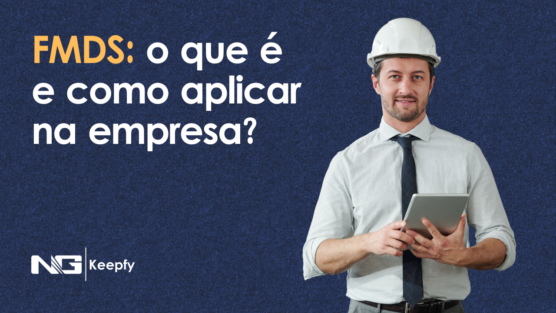
FMDS: o que é e como aplicar na empresa?
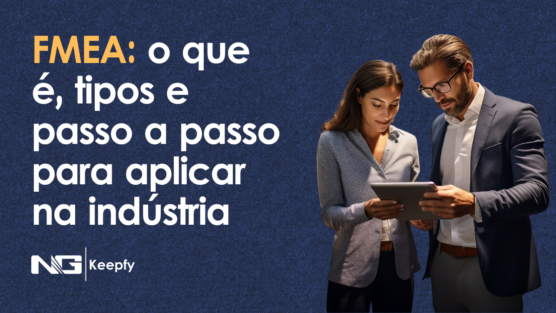