O dia a dia na gestão da manutenção é realmente impressionante. Tem tudo para ser tranquilo até que, quando menos se espera, chega a informação de que um dos equipamentos acabou de quebrar. E, adivinhe só, é justamente aquele de maior criticidade para o ciclo produtivo da empresa.
Você pensa: “O que pode ter acontecido? As manutenções estão em dia!”
Uma parte sua até pode continuar preocupada, mas você não permite que essa pequena adversidade abale a sua postura como gestor. Afinal, você sabe que desafios fazem parte da rotina de manutenção e pensar de cabeça quente não vai ajudar a resolver o problema.
Ainda que as adversidades sejam comuns dentro das indústrias, não podemos deixar de assumir que muitos obstáculos podem se tornar uma tremenda dor de cabeça para a equipe de manutenção. Mesmo que os profissionais realizem um controle eficaz sobre as atividades.
Quer conhecer quais são os maiores desafios da gestão da manutenção e como o gestor pode superar todas as dificuldades? Continue a leitura e descubra!
Os desafios da gestão de manutenção
Um dos motivos que mais desgastam os gestores de manutenção são as paradas não planejadas no processo produtivo – aquelas que poderiam ser evitadas caso alguns cuidados tivessem sido tomados antes, durante ou até mesmo depois da execução das manutenções.
Quando as manutenções não são feitas regularmente ou não são realizadas de forma efetiva, as chances de problemas são maiores. Por isso, para evitar que esses inconvenientes aconteçam, os gestores precisam garantir que os processos de manutenção sejam eficazes, mas também eficientes.
Abaixo, veja quais são os principais desafios da gestão de manutenção e como é possível superá-los.
1. Fornecedores de baixa qualidade
Um dos grandes desafios da gestão de manutenção é conseguir trabalhar com fornecedores de qualidade. Isso porque é bastante comum os gestores priorizarem o preço dos insumos, em vez de fazerem a avaliação correta dos produtos utilizados. Garantindo, assim, a compra apenas de materiais confiáveis.
Para superar esse problema é necessário monitorar possíveis desgastes precoces nas peças utilizadas e a vida útil de cada uma. Caso o resultado não tenha sido satisfatório, o ideal é que os gestores repitam os testes em peças de outras marcas ou outros fornecedores, para encontrarem o produto e parceiro ideal.
2. Falta de comunicação
A falta de comunicação pode parecer um problema pequeno, mas pode acabar se transformando em um empecilho enorme para os negócios. Isso porque, quando não há comunicação entre os setores, podem ocorrer paradas não planejadas ou até mesmo a perda da produtividade dentro da indústria.
O recomendado aqui é que se invista na melhoria da comunicação entre as equipes – com auxílio da tecnologia, por exemplo. Além disso, é fundamental investir em mudanças no mindset organizacional para que todos os envolvidos compreendam a importância de relatar os problemas e solicitar apoio.
A tecnologia pode ajudar a acabar com as dores de cabeça. Quer saber como? Conheça o Keepfy
3. Desorganização do setor
A desorganização é uma inimiga declarada da gestão de manutenção. Um setor que não tem procedimentos e instruções bem detalhadas pode “contribuir” para a perda de produtividade, de confiabilidade das informações e de disponibilidade dos equipamentos para o ciclo produtivo.
Nessa hora, os gestores se questionam: “Será que estamos aplicando práticas congruentes com os objetivos da empresa?”. Essa é, sem dúvida, uma pergunta que todos os profissionais precisam fazer antes de conseguirem direcionar as estratégias do setor para resultados positivos.
4. Não capacitação da equipe
Como um gestor espera aumentar a produtividade da equipe de manutenção se os profissionais não acompanham a evolução dos equipamentos nem da sua função? Para que os colaboradores consigam realizar o trabalho com eficiência, é indispensável que eles estejam habilitados e preparados.
Por isso, lembre-se de investir na capacitação dos colaboradores, inclusive na equipe de manutenção. Com um time engajado e amplamente preparado para os principais desafios do dia a dia, os resultados do setor e da empresa tendem a se tornar cada vez melhores.
5. Falta de planejamento
O setor de manutenção precisa estar alinhado ao planejamento estratégico da empresa. Sem um plano de trabalho é praticamente impossível que a equipe saiba o caminho correto a seguir, e sem direcionamento os objetivos nunca serão alcançados.
Para superar esse obstáculo, é preciso contar com o apoio do gestor de manutenção na integração com os demais líderes da empresa. Além disso, na criação de um plano de manutenção capaz de sustentar os objetivos da indústria como um todo.
6. Manutenções não planejadas
A manutenção não planejada é dividida em duas classes: manutenção corretiva não planejada, que envolve a correção de falhas após sua ocorrência, e manutenções ocasionais, que não seguem uma rotina e geralmente são realizadas nos intervalos de produção, paradas para almoço ou quando o equipamento está desligado.
As manutenções ocasionais não costumam acarretar custos elevados porque envolvem pequenos reparos e procedimentos simples. Entretanto, a manutenção corretiva não planejada pode implicar em altos custos, já que ocasiona perdas de produção e tende a gerar danos mais graves nos ativos.
Uma parada inusitada em um equipamento crítico, por exemplo, pode paralisar todo o processo produtivo, atrasar a fabricação dos itens e prejudicar prazos de entrega. Para superar esse desafio da gestão da manutenção, o ideal é que o profissional crie um plano preventivo eficaz para inibir possíveis falhas e erros.
7. Manutenções não programadas
Diferente das manutenções não planejadas, que são aplicadas em caráter emergencial, as manutenções não programadas consistem em tarefas que não estavam agendadas previamente de acordo com o tempo de disponibilidade da equipe.
Se o gestor não faz a programação correta das manutenções, levando em consideração o tempo, a alocação técnica e atividades que precisam ser realizadas nos equipamentos, o campo fabril pode ficar uma verdadeira bagunça. E, por fim, sofrer com paralisações.
Então, como resolver esse problema sério? O profissional deve organizar manutenções periódicas com base em apontamentos, disponibilidade de mão de obra e cuidados especiais necessários sobre cada ativo.
8. Processos manuais
Muitas empresas ainda realizam processos de análise e coleta de dados manualmente. Isso não é necessariamente errado, mas vale lembrar que operações manuais estão mais suscetíveis a erros já que envolvem trabalho humano.
Na manutenção de ativos todo cuidado é pouco, basta uma informação errada para afetar o direcionamento das atividades e a tomada de decisão. Por sorte, problemas como esses podem ser facilmente evitados se o setor tiver o apoio de uma ferramenta tecnológica.
Com um software de gestão, por exemplo, a indústria pode integrar os departamentos e reunir uma série de informações atualizadas sobre os ativos em um só lugar. Pode ainda acessar indicadores de desempenho (KPIs), que mostram o rendimento das máquinas, bem como monitorar o status de cada tarefa.
9. Aumentar a produtividade dos ativos
Cada máquina e equipamento possui um tempo de vida útil, mas isso não significa que a empresa é incapaz de estender esse período de validade ou aumentar a sua capacidade de produção.
A manutenção, quando aplicada corretamente, impede que problemas nas máquinas prejudiquem o processo produtivo. Mas, mais importante que isso, melhora a saúde dos ativos significativamente, deixando-os mais preparados para desempenhar suas funções com excelência.
Realizar a manutenção preventiva e manutenção preditiva são duas formas de aumentar a produtividade e vida útil das máquinas. Ajudam a reduzir e impedir falhas, bem como descobrir qual é a raiz dos defeitos.
10. Gerenciamento de tempo
A rotina do gestor de manutenção é repleta de atividades. Não envolve apenas monitorar os ativos e acompanhar a equipe responsável pelos reparos e consertos, mas falar com fornecedores, responder e-mails e se encontrar com a diretoria para discutir estratégias.
A questão é que a falta de gerenciamento de tempo e disponibilidade pode impactar os resultados no campo fabril, e impedir que a indústria tenha um desempenho melhor que o esperado.
Para conseguir superar esse desafio da gestão da manutenção e dar conta de todas as tarefas, o profissional precisa manter a sua rotina em dia. Deve estabelecer quais são suas prioridades, especialmente quanto às atividades do setor, e planejar a sua agenda de modo que consiga cumprir com todas suas funções.
11. Análise de dados e construção de relatórios
Os números e indicadores de desempenho são essenciais para o direcionamento do setor de manutenção. Eles mostram como está a real situação dos ativos, bem como a sua performance e rendimento no chão de fábrica.
A questão é que acessar informações atualizadas, construir relatórios de qualidade e analisar dados ainda são problemas comuns dentro do segmento. Isso pode estar relacionado aos processos manuais que as empresas ainda adotam, até a falta de tecnologia.
Se os gestores realmente querem superar esse desafio da gestão da manutenção e ter acesso a relatórios completos para melhorar a análise, precisam abraçar a transformação digital o quanto antes. E uma forma de fazerem isso é apostando em ferramentas mais modernas e inteligentes.
12. Necessidade de ferramentas mais modernas
Sabe-se que a manutenção deixou de ser um setor focado apenas em conservar equipamentos. Nos últimos tempos, os gestores passaram a tomar decisões importantes e que influenciam toda a cadeia produtiva. Isso porque acompanhar o desempenho das máquinas tem ajudado na formulação de melhores estratégias.
Soluções tecnológicas voltadas ao apoio deste novo conceito de manutenção são extremamente necessárias para acompanhar o desempenho. Ferramentas como o Keepfy têm permitido aos profissionais a conquista de resultados cada vez mais satisfatórios e consistentes na gestão, uma vez que integram setores, permitem análise de indicadores e otimizam processos.
Depois de ler todo o texto, podemos perceber que o dia a dia de um gestor de manutenção é e sempre será repleto de desafios. Entretanto, com apenas algumas medidas e o apoio de uma boa ferramenta tecnológica, já é possível minimizar as “dores de cabeça” da função e aumentar o alcance de resultados cada vez melhores no setor.
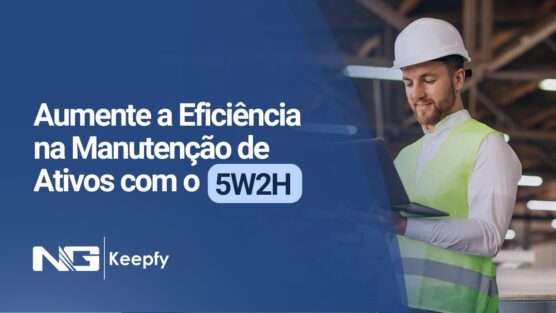
Aumente a Eficiência na Manutenção de Ativos com o 5W2H
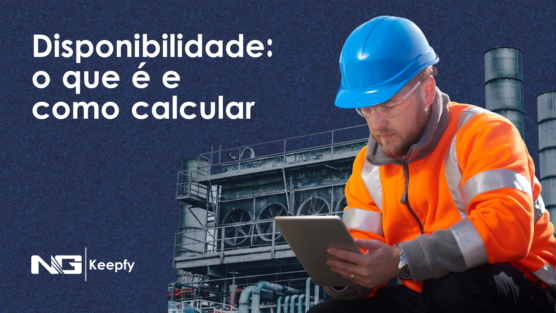
Disponibilidade: o que é e como calcular na manutenção
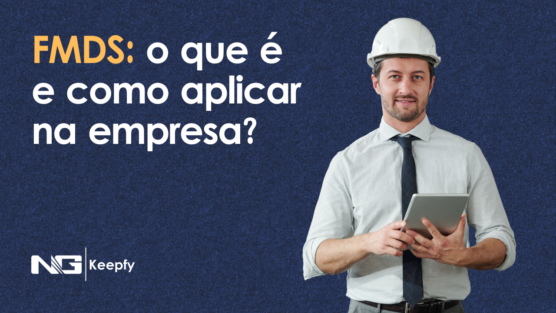
FMDS: o que é e como aplicar na empresa?
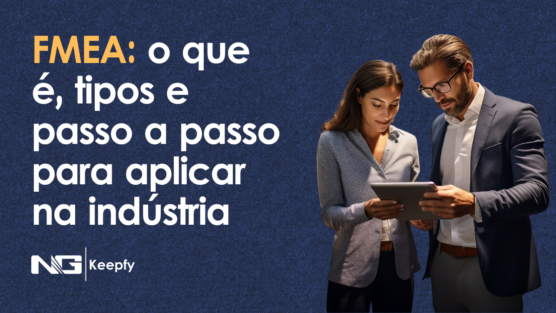
FMEA: o que é, tipos e passo a passo para aplicar na indústria
Conta pra gente!
o que você achou deste conteúdo? Escreva nos comentários.