No competitivo cenário industrial atual, uma parada inesperada na produção pode representar muito mais do que simplesmente interromper temporariamente os processos: significa perdas financeiras significativas, comprometimento de metas estratégicas e potencial erosão da competitividade empresarial.
Os gestores de manutenção sabem que cada minuto de inatividade não planejada traduz-se diretamente em custos diretos e indiretos que extrapolam os limites da área técnica. Desde a subutilização de recursos humanos até a interrupção de cadeias de suprimentos, as consequências de uma parada podem ser devastadoras para o desempenho organizacional.
Este artigo mergulhará na análise técnica detalhada dos impactos econômicos de paradas não programadas, apresentando metodologias práticas de cálculo, estratégias de mitigação de riscos e ferramentas essenciais para transformar a manutenção de um centro de custo em um departamento estratégico de geração de valor.
Nosso objetivo é demonstrar que investir em manutenção preventiva e preditiva não é um gasto, mas uma decisão inteligente de gestão que protege a performance e a lucratividade da organização.
Impactos Financeiros Diretos de uma Parada Não Planejada
A interrupção não programada de processos produtivos representa muito mais do que uma simples contingência operacional. Trata-se de um evento com potencial de causar danos significativos e multidimensionais à saúde financeira corporativa, cujos reflexos ultrapassam os limites imediatos da produção.
Perda de Produção e Faturamento
Cada minuto de parada representa uma equação complexa de prejuízos diretos e indiretos. A mensuração precisa desses impactos revela uma realidade financeira muitas vezes subestimada pelas organizações. Considerando empresas industriais de médio e grande porte, uma parada inesperada pode representar perdas que variam entre 5% a 20% do faturamento mensal, dependendo da criticidade do ativo e do setor de atuação.
A produtividade interrompida traduz-se instantaneamente em receitas não realizadas. Um equipamento estratégico parado significa não apenas produção suspensa, mas compromissos contratuais potencialmente descumpridos, multas por atraso e perda de competitividade no mercado. A capacidade de entrega, elemento fundamental na reputação empresarial, é diretamente impactada.
Custos de Mão de Obra e Horas Extras
A dinâmica de recuperação de uma parada não planejada aciona um mecanismo complexo de recomposição operacional. Técnicos, engenheiros e equipes de manutenção são mobilizados emergencialmente, gerando custos adicionais significativos em horas extras e regimes excepcionais de trabalho.
Estatisticamente, as horas extras decorrentes de manutenção corretiva podem elevar os custos de mão de obra em até 70% em relação ao planejamento original. Essa sobrecarga não se limita apenas ao aspecto financeiro, mas compromete a eficiência operacional e o planejamento estratégico da equipe técnica.
Desperdício de Matéria-Prima e Produtos em Processo
Uma parada inesperada provoca descontinuidade imediata nos processos produtivos, resultando em perdas materiais substanciais. Matérias-primas em processamento podem ser comprometidas, produtos semi-elaborados podem necessitar de descarte ou retrabalho, elevando exponencialmente os custos operacionais.
Em setores com processos contínuos, como químico, metalúrgico e alimentício, o desperdício pode representar perdas diretas entre 10% a 25% do valor total dos insumos em processo. A recuperação desses materiais nem sempre é possível, transformando a parada em um evento de impacto financeiro ainda mais expressivo.
A análise desses múltiplos aspectos evidencia que a manutenção preventiva não deve ser compreendida como um custo, mas como um investimento estratégico. A capacidade de antecipar, diagnosticar e intervir proativamente nos ativos representa a diferença entre a resiliência operacional e a vulnerabilidade financeira.
A manutenção deixa de ser uma função meramente técnica e se consolida como elemento fundamental na estratégia corporativa, com capacidade direta de proteção e otimização dos resultados organizacionais.
Impactos Indiretos e Custos Ocultos
A gestão de manutenção ultrapassa significativamente o simples reparo pontual de equipamentos. Os impactos de uma parada inesperada se ramificam por toda a cadeia produtiva, gerando consequências estratégicas que extrapolam o custo direto do reparo.
Atrasos nas Entregas e Insatisfação dos Clientes
Quando um equipamento falha inesperadamente, a primeira e mais crítica consequência recai sobre a cadeia de suprimentos. Os atrasos na produção provocam efeitos em cascata: prazos comprometidos, clientes insatisfeitos e potencial perda de credibilidade comercial. Estudos setoriais demonstram que cada hora de parada pode representar até 20% de redução na taxa de entrega, impactando diretamente a reputação organizacional.
A imprevisibilidade gerada por manutenções corretivas constantes deteriora a confiança dos clientes, criando um ciclo negativo de percepção de qualidade. Empresas com processos de manutenção preventiva estruturados conseguem reduzir atrasos em até 65%, mantendo níveis de serviço consistentes.
Desgaste Acelerado dos Equipamentos
Paradas não planejadas não representam apenas uma interrupção momentânea, mas catalisam um processo de degradação progressiva dos ativos. Cada acionamento emergencial submete os equipamentos a esforços adicionais, antecipando ciclos de desgaste e reduzindo significativamente a vida útil dos componentes.
A ausência de manutenção preventiva pode acelerar a depreciação dos equipamentos em até 40%, elevando custos de reposição e comprometendo a eficiência operacional. Máquinas submetidas a intervenções constantes e não programadas tendem a apresentar falhas mais frequentes e complexas, elevando exponencialmente os riscos operacionais.
Queda na Qualidade dos Produtos
A instabilidade operacional provocada por manutenções inadequadas impacta diretamente os padrões de qualidade. Equipamentos mal calibrados ou em condições operacionais instáveis produzem itens fora de especificação, gerando refugos, retrabalhos e potenciais perdas econômicas significativas.
Dados técnicos indicam que falhas não programadas podem elevar a taxa de produtos defeituosos em até 30%, representando não apenas perdas materiais diretas, mas comprometendo a reputação de qualidade da organização. A manutenção preventiva surge, portanto, como estratégia fundamental de garantia de qualidade.
A manutenção deixa de ser um centro de custo para se configurar como elemento estratégico de competitividade. Sua execução adequada não representa um gasto, mas um investimento direto na eficiência operacional, na satisfação do cliente e na sustentabilidade econômica do negócio.
Calculando o Custo Real de uma Parada Inesperada
A gestão eficiente de ativos industriais transcende a simples manutenção corretiva. Compreender o impacto financeiro real de uma parada inesperada representa um elemento estratégico fundamental para organizações que buscam maximizar sua produtividade e eficiência operacional.
Identificando as Variáveis Relevantes
O cálculo do custo total de uma parada inesperada demanda uma análise multidimensional que vai além dos gastos imediatos com reparo. As variáveis críticas incluem custos diretos de manutenção, perda de produção, horas-homem não produtivas e impactos indiretos na cadeia produtiva.
Os componentes principais deste cálculo compreendem: – Custo de reparo do equipamento – Receita não gerada durante a parada – Custos operacionais fixos mantidos – Horas extras de reposição de produção – Potencial perda de qualidade e retrabalho – Penalidades contratuais por não entrega
Aplicando uma Fórmula de Cálculo
A metodologia de cálculo do custo total de parada pode ser representada pela seguinte expressão:
Custo Total = (Custo Direto de Reparo) + (Receita Perdida) + (Custos Operacionais) + (Impactos Indiretos)
Esta fórmula permite uma quantificação sistêmica que revela o verdadeiro impacto financeiro de uma interrupção não planejada.
Exemplo Prático e Estimativa de Custo
Consideremos um cenário industrial típico de uma linha de produção de médio porte. Uma parada inesperada de 12 horas em um equipamento crítico pode representar custos significativos.
Análise detalhada: – Custo direto de reparo: R$ 15.000 – Receita perdida por hora: R$ 25.000 – Custos operacionais fixos: R$ 5.000 – Horas extras de reposição: R$ 8.000 – Potencial perda de qualidade: R$ 12.000
Cálculo consolidado: (15.000) + (25.000 x 12) + (5.000) + (8.000) + (12.000) = R$ 436.000
Este exemplo demonstra que uma parada aparentemente pontual pode resultar em prejuízos substanciais, justificando investimentos robustos em manutenção preditiva e gestão preventiva de ativos.
A verdadeira essência desta análise não reside apenas nos números, mas na compreensão estratégica de que manutenção é um investimento, não um custo. Cada real aplicado em prevenção pode representar múltiplos em economia e eficiência operacional.
A abordagem sistemática e analítica transforma a manutenção de uma função operacional para uma função estratégica, alinhando diretamente performance técnica com resultados financeiros corporativos.
Estratégias para Evitar Paradas Não Planejadas
A gestão eficiente de ativos industriais transcende a simples manutenção corretiva, configurando-se como uma estratégia fundamental para a competitividade empresarial. Paradas não planejadas representam não apenas perdas financeiras diretas, mas comprometem toda a cadeia de produtividade organizacional.
Manutenção Preventiva e Preditiva: Antecipação como Princípio
A implementação de estratégias preventivas constitui o primeiro pilar para mitigar riscos de interrupções operacionais. Diferentemente da manutenção corretiva, que atua após a falha, as abordagens preventiva e preditiva trabalham com antecipação e diagnóstico precoce de potenciais anomalias.
Técnicas como análise de vibração, termografia e monitoramento de condição permitem identificar desvios sutis antes que evoluam para falhas críticas. Essas metodologias possibilitam programar intervenções precisas, reduzindo significativamente o risco de paradas súbitas e custosas.
A aplicação de manutenção preditiva baseada em dados representa um avanço tecnológico que integra sensores, análise estatística e inteligência artificial para prever comportamentos dos equipamentos. Essa abordagem transforma a manutenção de um centro de custo para um gerador de valor estratégico.
Gestão Eficiente de Estoques de Peças de Reposição
O gerenciamento inteligente de peças sobressalentes é crítico para minimizar tempos de parada. Estratégias como inventário just-in-time e análise de criticidade permitem dimensionar estoques com precisão, equilibrando disponibilidade e custo de armazenamento.
Sistemas de gestão de materiais integrados possibilitam rastreabilidade em tempo real, permitindo identificar rapidamente componentes necessários para reparo. A digitalização desses processos reduz significativamente janelas de indisponibilidade e otimiza recursos financeiros.
Treinamento e Capacitação das Equipes de Manutenção
Capital humano representa o elemento diferenciador em qualquer estratégia de manutenção. Equipes tecnicamente preparadas conseguem diagnosticar, intervir e prevenir falhas com muito mais eficiência.
Programas estruturados de capacitação técnica que combinam treinamento teórico e prático, certificações especializadas e desenvolvimento de competências específicas elevam exponencialmente a performance das equipes. O investimento em desenvolvimento profissional traduz-se diretamente em maior confiabilidade operacional.
A integração de conhecimento técnico com tecnologias digitais como simuladores, realidade aumentada e plataformas de treinamento online potencializa o aprendizado, criando profissionais multidisciplinares capazes de compreender sistemas cada vez mais complexos.
Paradas não planejadas não são acidentes, mas sintomas de gestão reativa. Organizações que compreendem manutenção como função estratégica, investindo em prevenção, tecnologia e desenvolvimento humano, conquistam níveis superiores de eficiência operacional e competitividade sustentável.
A manutenção moderna transcende procedimentos técnicos: configura-se como elemento central na geração de valor, performance e resiliência organizacional.
A Importância Estratégica da Manutenção
A manutenção deixou de ser uma atividade meramente corretiva para se tornar um componente fundamental na estratégia operacional das organizações modernas. Sua relevância transcende a simples preservação de equipamentos, configurando-se como um elemento crítico para a competitividade empresarial.
Garantindo a Continuidade Operacional
A continuidade operacional representa o coração pulsante de qualquer processo produtivo. Paradas inesperadas não são apenas interrupções temporárias, mas verdadeiros vetores de perdas financeiras significativas. Estudos setoriais demonstram que cada hora de paralisação pode representar prejuízos que variam entre 10% a 30% do valor horário de produção, dependendo da complexidade do sistema industrial.
A gestão proativa da manutenção permite antecipar potenciais falhas, implementando estratégias preventivas que minimizam riscos de interrupções. Através de análises preditivas e monitoramento contínuo, as equipes técnicas podem identificar sinais preliminares de desgaste ou anomalias antes que estas evoluam para quebras efetivas.
Reduzindo Custos e Aumentando a Lucratividade
A manutenção eficiente configura-se como um poderoso instrumento de otimização econômica. Investimentos sistemáticos em manutenção preventiva podem reduzir custos operacionais em até 40%, comparativamente a modelos puramente corretivos. A lógica é simples: reparos antecipados são significativamente menos onerosos que substituições totais de equipamentos.
Métricas como Overall Equipment Effectiveness (OEE) evidenciam essa relação direta entre manutenção e desempenho financeiro. Organizações que implementam metodologias estruturadas de gestão de ativos conseguem elevar sua eficiência global em percentuais que variam entre 15% e 25%, impactando diretamente a margem de lucro.
Manutenção como Vantagem Competitiva
No cenário empresarial contemporâneo, a capacidade de manter ativos em condições operacionais ótimas diferencia organizações. Uma estratégia de manutenção robusta não representa apenas um centro de custos, mas um gerador de valor competitivo.
Empresas que dominam técnicas avançadas de gestão de ativos conseguem antecipar necessidades de intervenção, reduzir tempos de parada e otimizar ciclos de vida útil de equipamentos.
A transformação da manutenção de um departamento operacional para um núcleo estratégico demanda investimento contínuo em capacitação técnica, tecnologia e metodologias analíticas. O resultado não é apenas a preservação de ativos, mas a construção de um ecossistema operacional resiliente e eficiente.
A manutenção moderna transcende a perspectiva tradicional de reparo, configurando-se como um elemento fundamental para a sustentabilidade e competitividade organizacional. Sua relevância estratégica está diretamente conectada à capacidade de gerar valor, reduzir riscos e potencializar performance.
Transformando Paradas Inesperadas em Oportunidades Estratégicas
As paradas inesperadas na produção não são apenas interrupções operacionais, mas verdadeiros vetores de perdas financeiras silenciosas. Nosso mergulho técnico revelou que cada minuto de inatividade não planejada representa não apenas custos diretos, mas um comprometimento sistêmico da eficiência organizacional.
A manutenção deixou de ser um departamento operacional para se consolidar como núcleo estratégico de competitividade. Investir em práticas preventivas, análise preditiva e cultura de confiabilidade não é um custo, mas um investimento com retorno mensurável. Gestores que compreendem essa transformação passam de “apagadores de incêndio” a verdadeiros arquitetos da performance empresarial.
Paradas inesperadas não são fatalidades, são oportunidades de redesenhar a excelência operacional. A manutenção moderna não pergunta “quando o equipamento quebrará?”, mas “como podemos garantir que ele sempre funcione?”.
Experimente o Keepfy grátis por 7 dias e evite paradas inesperadas em sua indústria.
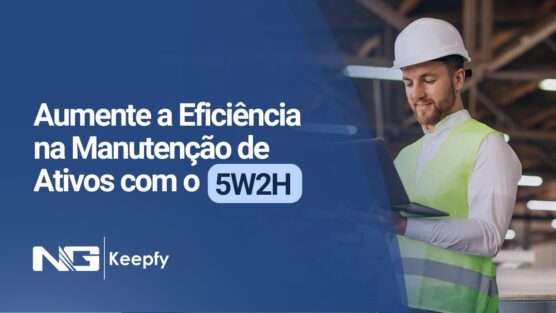
Aumente a Eficiência na Manutenção de Ativos com o 5W2H
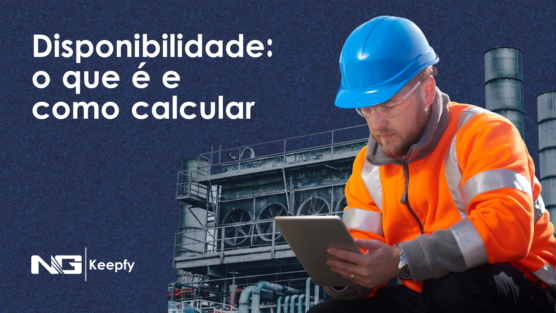
Disponibilidade: o que é e como calcular na manutenção
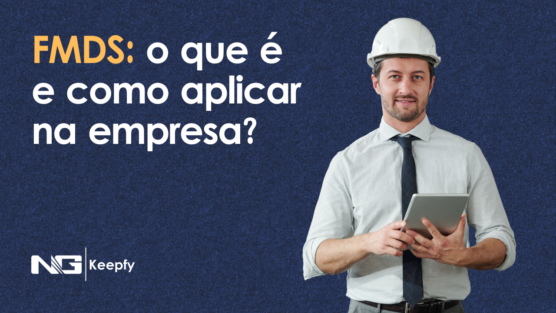
FMDS: o que é e como aplicar na empresa?
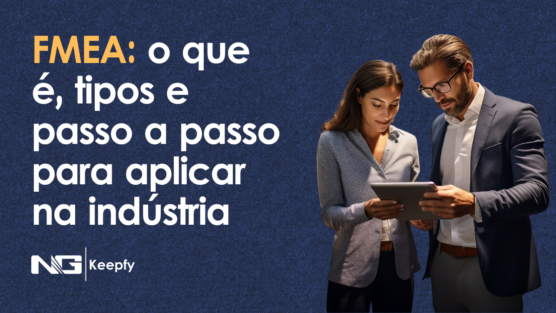