No complexo universo da gestão industrial, a manutenção eficiente não é apenas um diferencial, mas uma necessidade crítica para a produtividade e competitividade. Um checklist de manutenção bem estruturado pode ser o primeiro passo decisivo para transformar processos operacionais fragmentados em um sistema coeso e controlado.
A maioria das organizações industriais enfrenta desafios significativos na gestão de ativos: paradas não programadas, manutenções corretivas excessivas e perda de eficiência operacional. Um checklist sistemático permite não apenas mitigar esses riscos, mas também estabelecer uma metodologia padronizada de gerenciamento de manutenção que otimiza recursos, reduz custos e aumenta a confiabilidade dos equipamentos.
Este artigo apresentará um checklist básico e estratégico, desenvolvido para auxiliar gestores de manutenção a iniciarem uma transformação organizacional. Abordaremos elementos fundamentais como cadastro de equipamentos, histórico de manutenções, periodicidade de intervenções, documentação técnica e indicadores de desempenho, fornecendo um roteiro prático para estruturação de processos maduros de manutenção.
Identificar e Catalogar os Ativos Críticos
A gestão eficiente de manutenção começa com um mapeamento preciso dos ativos industriais. Identificar e classificar corretamente os equipamentos é fundamental para desenvolver estratégias de manutenção assertivas e minimizar riscos operacionais.
Definir Critérios de Criticidade
A determinação da criticidade dos ativos representa o primeiro passo estratégico para priorizar investimentos e esforços de manutenção. Este processo envolve uma análise multidimensional que considera aspectos como impacto na produção, segurança, custos de parada e complexidade de substituição.
Os principais critérios para avaliação de criticidade incluem:
Impacto Operacional: Capacidade do equipamento de interromper completamente a produção em caso de falha. Ativos que provocam paradas totais ou significativas recebem pontuação mais alta.
Custo de Indisponibilidade: Mensuração financeira do prejuízo gerado pela interrupção do equipamento, considerando perdas de produção, horas-homem e potencial perda de clientes.
Complexidade de Manutenção: Avaliação da dificuldade técnica para realizar reparos, incluindo disponibilidade de peças, necessidade de mão de obra especializada e tempo de reparo.
Segurança: Análise do potencial de risco à integridade física dos operadores e ao ambiente em caso de falha do equipamento.
Criar um Sistema de Codificação de Ativos
Um sistema estruturado de codificação permite identificação rápida e inequívoca de cada ativo, facilitando gestão, rastreabilidade e histórico de manutenções. A codificação deve ser desenvolvida considerando características específicas da planta industrial.
Estrutura recomendada para codificação: – Localização física – Família/tipo de equipamento – Número sequencial – Ano de instalação
Exemplo: PROD-MOT-025-2018 (Produção – Motor – Número sequencial 25 – Ano 2018)
Registrar Informações Técnicas dos Equipamentos
O registro detalhado de especificações técnicas constitui base fundamental para planejamento de manutenções preventivas e preditivas. Cada ativo deve possuir um dossiê técnico contendo informações essenciais.
Documentação técnica deve incluir: – Fabricante e modelo – Especificações técnicas – Capacidade nominal – Histórico de manutenções – Peças de reposição – Manuais originais – Características operacionais – Registros de desempenho
A digitalização destes registros em sistemas Enterprise Asset Management (EAM) ou Computerized Maintenance Management System (CMMS) permite gerenciamento integrado e análises preditivas.
A implementação sistemática destas práticas transforma a manutenção de uma atividade reativa para uma abordagem estratégica, antecipando falhas e otimizando a performance dos ativos industriais.
Estabelecer um Plano de Manutenção Preventiva
A implementação de um plano de manutenção preventiva estruturado é fundamental para garantir a confiabilidade e eficiência operacional dos ativos industriais. Este processo requer uma abordagem sistemática e estratégica que considere as particularidades de cada equipamento e ambiente fabril.
Determinar a Frequência das Atividades de Manutenção
A definição precisa da periodicidade das intervenções preventivas demanda uma análise criteriosa baseada em múltiplos fatores. Recomenda-se inicialmente realizar um mapeamento detalhado de cada ativo, considerando suas características técnicas, histórico de falhas, criticidade operacional e recomendações dos fabricantes.
Os intervalos de manutenção devem ser estabelecidos através de uma combinação de análises técnicas, incluindo tempo médio entre falhas (MTBF), dados de desempenho histórico e especificações técnicas originais. Equipamentos com alta criticidade e impacto direto na produção necessitam de ciclos mais frequentes de inspeção e intervenção preventiva.
Criar Procedimentos Padrão para Cada Tipo de Equipamento
A padronização dos procedimentos de manutenção representa um elemento crucial para garantir consistência e qualidade nas intervenções. Cada categoria de equipamento deve possuir um protocolo específico que detalhe:
- Sequência de inspeção e verificação
- Pontos críticos de análise
- Ferramental necessário
- Parâmetros técnicos de referência
- Critérios de aceitação e rejeição
A documentação destes procedimentos deve ser desenvolvida de forma técnica, mas compreensível, permitindo que diferentes profissionais executem as atividades com o mesmo nível de precisão. Recomenda-se a utilização de linguagem clara, fluxogramas e, quando possível, recursos visuais que facilitem o entendimento.
Definir Responsabilidades e Qualificações da Equipe
A eficácia do plano de manutenção preventiva está diretamente relacionada à competência e comprometimento da equipe técnica. É essencial estabelecer um modelo de gestão de competências que contemple:
Requisitos técnicos para cada função, considerando níveis de senioridade e especialização específica para diferentes tipos de equipamentos. A capacitação deve ser contínua, com treinamentos periódicos que abordem tanto aspectos técnicos quanto metodológicos.
A definição de responsabilidades deve ser clara e documentada, estabelecendo atribuições específicas para cada nível hierárquico. O gestor de manutenção terá papel fundamental no planejamento estratégico, enquanto técnicos e analistas executarão as atividades operacionais.
A implementação deste modelo requer um sistema de gestão do conhecimento que promova o compartilhamento de informações, documentação de lições aprendidas e desenvolvimento constante das competências individuais e coletivas.
A construção de um plano de manutenção preventiva não é um projeto pontual, mas um processo contínuo de aprimoramento. A flexibilidade para adaptar procedimentos, a partir de dados e evidências técnicas, será determinante para o sucesso da estratégia de gestão de ativos.
Implementar um Sistema de Gestão da Manutenção
A implementação de um sistema de gestão da manutenção representa um marco crucial para a transformação da estratégia mantenedora de uma organização. Este processo demanda planejamento criterioso e execução meticulosa para garantir resultados efetivos.
Selecionar um Software de Gestão da Manutenção Adequado
A escolha do software de manutenção configura-se como etapa estratégica fundamental. Gestores devem avaliar soluções que contemplem requisitos específicos de sua operação, considerando variáveis como complexidade do parque industrial, número de ativos e recursos financeiros disponíveis.
Critérios essenciais para seleção incluem: compatibilidade com sistemas existentes, facilidade de integração, escalabilidade, geração de relatórios gerenciais e suporte técnico especializado. Recomenda-se priorizar plataformas que permitam cadastro detalhado de ativos, programação de manutenções preventivas e registro de histórico de intervenções.
Sistemas como o NG Keepfy e o NG Manutenção de Ativos (exclusivo para ERP Protheus) apresentam funcionalidades robustas para diferentes perfis industriais. A decisão deve contemplar demonstrações práticas, período de teste e alinhamento com a estratégia de manutenção da empresa.
Cadastrar Ativos e Planos de Manutenção no Sistema
O cadastramento preciso de ativos constitui base para gestão eficiente. Cada equipamento deve ser registrado com informações técnicas completas: características construtivas, especificações do fabricante, histórico de manutenções, documentação técnica e criticidade operacional.
A estruturação dos planos de manutenção demanda mapeamento detalhado dos intervalos de intervenção, definição de rotinas preventivas, identificação de componentes críticos e parametrização de frequências de manutenção. É fundamental registrar:
- Especificações técnicas dos equipamentos
- Histórico de falhas e intervenções
- Periodicidade recomendada de manutenções
- Peças de reposição
- Requisitos de segurança operacional
A migração de dados históricos e a padronização das informações garantem consistência e confiabilidade do sistema.
Treinar a Equipe para Utilizar o Sistema Corretamente
A capacitação técnica representa elemento diferencial para sucesso da implementação. O treinamento deve contemplar aspectos operacionais e estratégicos, desenvolvendo competências para utilização plena do software.
Recomenda-se estruturar programa de treinamento com abordagem prática, envolvendo:
- Navegação no sistema
- Registro de ordens de serviço
- Geração de relatórios gerenciais
- Alimentação de banco de dados
- Interpretação de indicadores de manutenção
A formação deve ser modular, considerando diferentes níveis hierárquicos – técnicos, supervisores e gestores – com conteúdo customizado para cada perfil.
O investimento em capacitação continuada potencializa a absorção tecnológica, promove cultura de melhoria contínua e maximiza retorno sobre investimento no sistema de gestão.
A implementação sistemática dessas etapas permite transformar práticas manutentivas, elevando patamares de eficiência operacional e competitividade industrial.
Estabelecer Indicadores de Desempenho da Manutenção
A implementação de indicadores de desempenho (KPIs) constitui elemento fundamental para a gestão eficaz da manutenção industrial. Sem métricas precisas, os gestores operam em um ambiente de incertezas, comprometendo a tomada de decisões estratégicas e a otimização dos processos.
Definir KPIs Relevantes para a Operação
A seleção de Key Performance Indicators (KPIs) deve ser criteriosa e alinhada aos objetivos específicos da organização. Indicadores como Tempo Médio Entre Falhas (MTBF), Tempo Médio de Reparo (MTTR), Disponibilidade de Equipamentos e Custo de Manutenção fornecem insights críticos sobre a performance dos ativos.
O MTBF, por exemplo, permite avaliar a confiabilidade dos equipamentos, indicando intervalos entre paradas não programadas. Já o MTTR mensura a eficiência das equipes técnicas no restabelecimento operacional, sinalizando potenciais necessidades de treinamento ou adequação de processos.
Configurar a Coleta e Análise dos Dados
A implementação de sistemas informatizados de gestão da manutenção (CMMS) representa estratégia essencial para coleta sistemática e análise de dados. Esses sistemas possibilitam registro detalhado de intervenções, histórico de manutenções, consumo de peças e tempos de parada.
A parametrização adequada do sistema deve contemplar: – Registro preciso de todas as ordens de serviço – Classificação detalhada de paradas e falhas – Vinculação de custos associados às intervenções – Geração automática de relatórios gerenciais
A qualidade do dado registrado impacta diretamente a precisão das análises e, consequentemente, a tomada de decisões estratégicas.
Realizar Reuniões Periódicas para Avaliar Indicadores
A análise crítica dos indicadores demanda encontros sistemáticos envolvendo equipes operacionais e gerenciais. Essas reuniões devem transcender a simples apresentação de números, promovendo discussões estruturadas sobre causas de desvios e proposição de planos de ação.
Recomenda-se periodicidade mensal, com agenda estruturada: – Apresentação consolidada dos indicadores – Análise comparativa com metas estabelecidas – Identificação de tendências e padrões – Proposição de ações corretivas – Acompanhamento de planos anteriormente definidos
A cultura de transparência e melhoria contínua emerge dessa prática, transformando dados em inteligência operacional.
A construção de um sistema de indicadores robusto não representa apenas um exercício estatístico, mas uma ferramenta estratégica de gestão. Permite visualizar com precisão a saúde dos ativos, otimizar recursos e sustentar decisões fundamentadas no ambiente industrial contemporâneo.
Promover a Melhoria Contínua do Processo de Manutenção
A melhoria contínua representa um pilar fundamental na gestão moderna de manutenção industrial, transcendendo a simples correção de falhas para se estabelecer como uma estratégia sistemática de evolução operacional. Implementar um modelo estruturado de aprimoramento constante permite que gestores de manutenção transformem desafios em oportunidades de desenvolvimento organizacional.
Identificar Oportunidades de Melhoria com Base nos KPIs
A identificação precisa de oportunidades de melhoria demanda uma análise criteriosa dos Key Performance Indicators (KPIs) de manutenção. Métricas como Tempo Médio Entre Falhas (MTBF), Tempo Médio de Reparo (MTTR), Disponibilidade de Equipamentos e Taxa de Falhas Críticas fornecem insights fundamentais sobre a performance dos ativos e processos.
A análise desses indicadores permite diagnosticar padrões de falha, gargalos operacionais e ineficiências sistêmicas. Gestores devem estabelecer uma sistemática de monitoramento periódico, preferencialmente com ferramentas que possibilitem visualização resultados.
Envolver a Equipe na Solução de Problemas e Otimização do Processo
O engajamento da equipe técnica constitui elemento crítico para o sucesso de iniciativas de melhoria contínua. Profissionais que atuam diretamente na operação e manutenção possuem conhecimento tácito valioso sobre os desafios cotidianos dos equipamentos.
Implementar metodologias como Círculos de Controle de Qualidade e Grupos de Resolução de Problemas permite capturar e sistematizar o conhecimento operacional. Sessões estruturadas de brainstorming, análise de causa-raiz e proposição de soluções devem ser incentivadas e formalizadas, criando um ambiente de colaboração e inovação.
A cultura de melhoria contínua se desenvolve quando os profissionais compreendem que suas contribuições são valorizadas e podem impactar diretamente a eficiência operacional. Reconhecimento e incentivos para propostas inovadoras funcionam como poderosos catalisadores de engajamento.
Documentar e Padronizar as Melhorias Implementadas
A documentação representa o elemento de consolidação e perenidade das melhorias identificadas. Cada solução implementada deve ser criteriosamente registrada, contemplando detalhes como contexto da melhoria, metodologia aplicada, resultados obtidos e lições aprendidas.
Procedimentos operacionais padrão (POPs) devem ser sistematicamente atualizados, incorporando as novas práticas e conhecimentos desenvolvidos. Ferramentas como Gestão Eletrônica de Documentos facilitam o versionamento e a disseminação padronizada das informações.
A padronização não significa engessamento, mas sim estabelecimento de uma base consistente sobre a qual inovações podem ser construídas. Cada melhoria documentada torna-se um novo ponto de referência para futuras otimizações, criando um ciclo virtuoso de aprendizado organizacional.
A implementação de um sistema estruturado de melhoria contínua exige comprometimento da liderança, investimento em capacitação e uma visão sistêmica que transcenda abordagens reativas de manutenção. Quando executada de forma consistente, essa estratégia transforma a área de manutenção de um centro de custos em um núcleo estratégico de geração de valor para a organização.
Transformando Checklists em Estratégia de Excelência Operacional
O checklist de manutenção não é apenas uma ferramenta burocrática, mas um poderoso instrumento de transformação organizacional. Ao implementar sistematicamente os pontos discutidos, os gestores de manutenção criam uma base sólida para elevar a performance dos ativos, reduzir paradas não programadas e otimizar recursos investidos.
A jornada para uma gestão de manutenção estruturada começa com pequenos passos metodológicos. Cada item do checklist representa um avanço estratégico na cultura de manutenção preventiva, permitindo que equipes passem de uma postura reativa para uma abordagem proativa e preditiva. A documentação adequada, o registro histórico e o planejamento sistemático são os pilares que sustentam a confiabilidade operacional.
Lembre-se que checklists não são correntes, mas asas que elevam a performance industrial. Sua implementação criteriosa é o primeiro passo para transformar a manutenção de um centro de custo em um gerador de valor estratégico.
Experimente o Keepfy grátis por 7 dias e coloque sua fábrica em ordem.
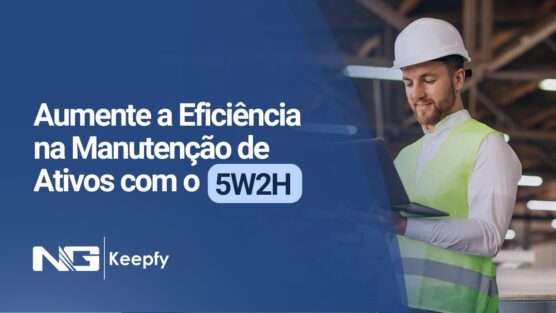
Aumente a Eficiência na Manutenção de Ativos com o 5W2H
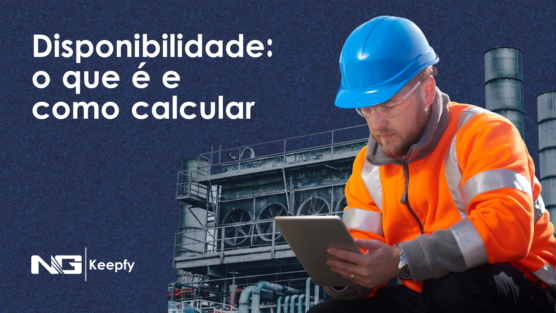
Disponibilidade: o que é e como calcular na manutenção
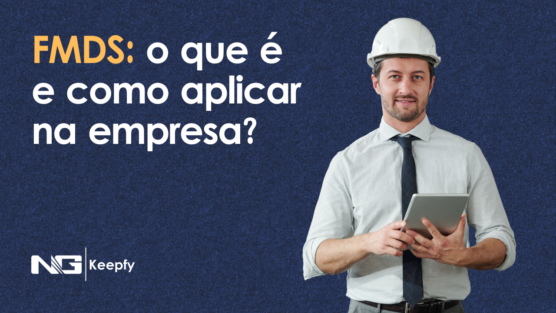
FMDS: o que é e como aplicar na empresa?
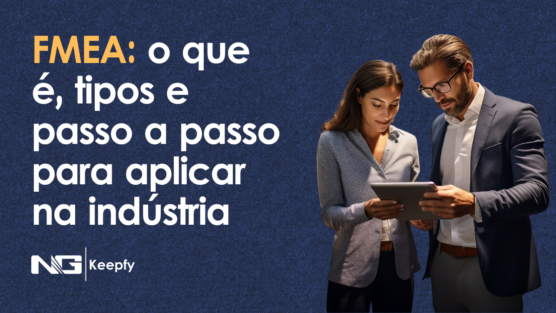