A metodologia japonesa 5S foi desenvolvida com o objetivo de promover a organização e a limpeza no ambiente de trabalho. Essa abordagem é amplamente utilizada em diversas indústrias, pois proporciona uma série de benefícios, incluindo aumento da eficiência operacional e melhoria na qualidade dos processos.
Neste artigo, discutiremos como implementar o 5S na manutenção industrial e como essa prática pode otimizar o desempenho e a organização dos setores de manutenção.
Passo a passo para a implementação do 5S
A implementação do 5S na manutenção industrial segue um processo estruturado, composto por cinco etapas. Essas etapas são:
- Seiri (Senso de Utilização): Nessa etapa, é necessário realizar uma análise criteriosa de todos os objetos e materiais presentes no ambiente de trabalho. O objetivo é identificar e eliminar itens desnecessários, como ferramentas quebradas, peças obsoletas, entre outros. Ao reduzir a quantidade de itens desnecessários, é possível liberar espaço e otimizar os processos de manutenção.
- Seiton (Senso de Organização): Após eliminar os itens desnecessários, é necessário organizar os objetos e materiais restantes. Nessa etapa, recomenda-se utilizar etiquetas, prateleiras e armários para categorizar e facilitar o acesso aos itens. Também é importante definir um local adequado para cada item, de forma a manter a organização e evitar desperdícios de tempo na busca por ferramentas e materiais.
- Seiso (Senso de Limpeza): A limpeza é um aspecto crucial para garantir um ambiente de trabalho seguro e eficiente. Nessa etapa, é necessário estabelecer rotinas de limpeza e manutenção, treinar os colaboradores para realizar essas atividades e manter os equipamentos e áreas de trabalho limpos e livres de sujeira. Além disso, é importante ter um plano de descarte adequado para resíduos gerados durante o processo de manutenção.
- Seiketsu (Senso de Padronização): O senso de padronização envolve a criação de padrões e procedimentos que garantam a manutenção e continuidade das práticas anteriores. Nessa etapa, é necessário estabelecer normas, checklist, cronogramas e treinamentos para assegurar que as práticas de organização, limpeza e utilização adequada dos recursos sejam aplicadas de forma consistente.
- Shitsuke (Senso de Autodisciplina): O último passo do processo envolve a criação de uma cultura de autodisciplina, na qual todos os colaboradores têm responsabilidade de manter as práticas do 5S. Isso requer um esforço contínuo de treinamento e conscientização, para que todos entendam a importância da implementação do 5S e se comprometam a seguir os princípios estabelecidos.
Benefícios do 5S na manutenção industrial
A implementação do 5S na manutenção industrial traz uma série de benefícios significativos para a empresa. Alguns dos principais benefícios incluem:
- Melhoria da eficiência: Ao eliminar itens desnecessários, organizar o espaço de trabalho e estabelecer padrões e procedimentos claros, a manutenção industrial se torna mais eficiente, reduzindo o tempo de execução das tarefas e aumentando a produtividade.
- Redução de custos: A aplicação do 5S na manutenção industrial contribui para a redução de desperdícios, como a compra de ferramentas duplicadas ou a perda de tempo buscando materiais desorganizados. Isso resulta em uma diminuição dos custos operacionais.
- Melhoria da segurança: Uma área de trabalho organizada e limpa ajuda a prevenir acidentes e doenças ocupacionais. O senso de limpeza e o descarte adequado de resíduos garantem um ambiente mais seguro para os colaboradores.
- Aumento da qualidade: A implementação do 5S na manutenção industrial implica em processos mais padronizados e controlados, resultando em uma melhoria na qualidade dos serviços prestados. Isso contribui para o aumento da satisfação do cliente e a competitividade da empresa.
Importância da organização no ambiente industrial
A organização é um fator crucial para o sucesso da manutenção industrial. Um ambiente desorganizado pode levar a atrasos, erros e desperdícios. Além disso, dificulta o acesso a ferramentas e materiais, tornando o trabalho mais difícil e demorado.
Manter o local de trabalho organizado proporciona melhores condições para o desenvolvimento das atividades de manutenção, evitando problemas e retrabalho. Além disso, uma empresa que preza pela organização transmite uma imagem profissional e confiável para os seus clientes.
Como otimizar a limpeza na manutenção industrial
A limpeza é um aspecto fundamental da manutenção industrial. Para otimizar esse processo, é importante seguir algumas práticas. Algumas dicas para otimizar a limpeza na manutenção industrial são:
- Definir uma rotina: Estabeleça uma rotina de limpeza diária, semanal e mensal. Isso ajuda a garantir que todas as áreas sejam limpas regularmente e mantidas em boas condições.
- Capacitar os colaboradores: Realize treinamentos para ensinar os colaboradores a realizar a limpeza de forma correta, utilizando os produtos e equipamentos adequados. Isso garante que todos saibam como executar as tarefas de limpeza de maneira eficiente e segura.
- Definir responsabilidades: Atribua responsabilidades claras para cada colaborador em relação à limpeza. Isso evita conflitos e garante que todas as áreas sejam devidamente cuidadas.
- Manter a organização: Utilize prateleiras, etiquetas e armários para organizar todos os materiais e ferramentas. Isso facilita a limpeza e evita a acumulação de sujeira em locais de difícil acesso.
A importância da autodisciplina no 5S para a manutenção
A autodisciplina desempenha um papel fundamental na implementação e manutenção do 5S na manutenção industrial. É importante que todos os colaboradores estejam engajados e comprometidos em seguir as práticas do 5S de forma consistente.
A autodisciplina envolve responsabilidade individual e a capacidade de autogerenciamento. Para promover a autodisciplina no 5S, é essencial:
- Treinar e conscientizar: Realize treinamentos regulares para reforçar a importância do 5S e conscientizar os colaboradores sobre seus benefícios. Explique como a autodisciplina contribui para a efetividade do 5S.
- Reconhecimento e incentivo: Reconheça e recompense os colaboradores que demonstram um bom desempenho na prática do 5S. Incentive o compartilhamento de experiências e melhores práticas entre os membros da equipe.
- Monitoramento e revisão: Estabeleça processos para monitorar e avaliar regularmente o cumprimento das práticas do 5S. Realize auditorias internas para identificar oportunidades de melhoria e revisar continuamente os procedimentos.
Conclusão
A implementação do 5S na manutenção industrial é uma prática essencial para promover a organização, eficiência e segurança nos processos.
Ao seguir o passo a passo do 5S e valorizar a autodisciplina, as empresas podem obter uma série de benefícios, como a melhoria da eficiência, redução de custos, aumento da qualidade e segurança no ambiente de trabalho.
Portanto, vale a pena investir na implementação do 5S e aproveitar essas vantagens para otimizar a manutenção industrial.
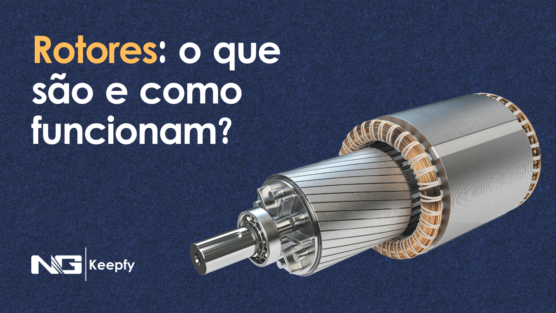
Rotores: o que são e como funcionam?
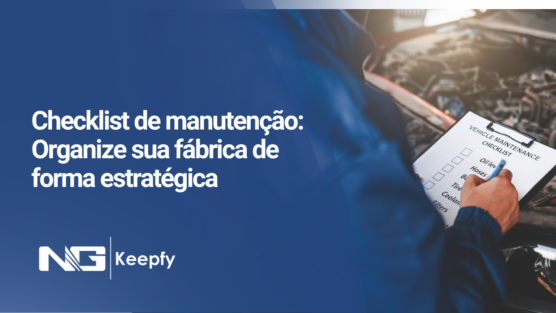
Checklist de manutenção: Organize sua fábrica de forma estratégica
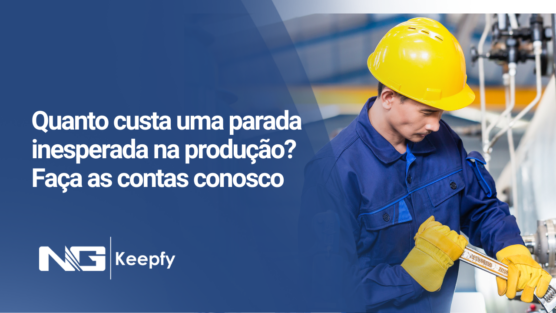
Quanto custa uma parada inesperada na produção? Faça as contas conosco
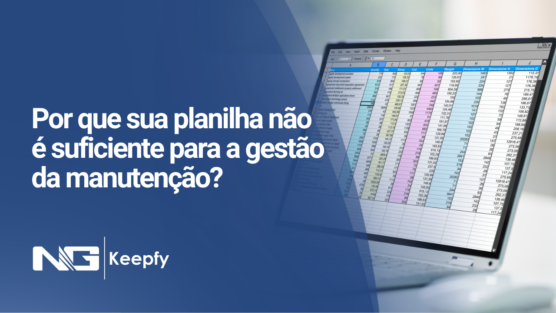